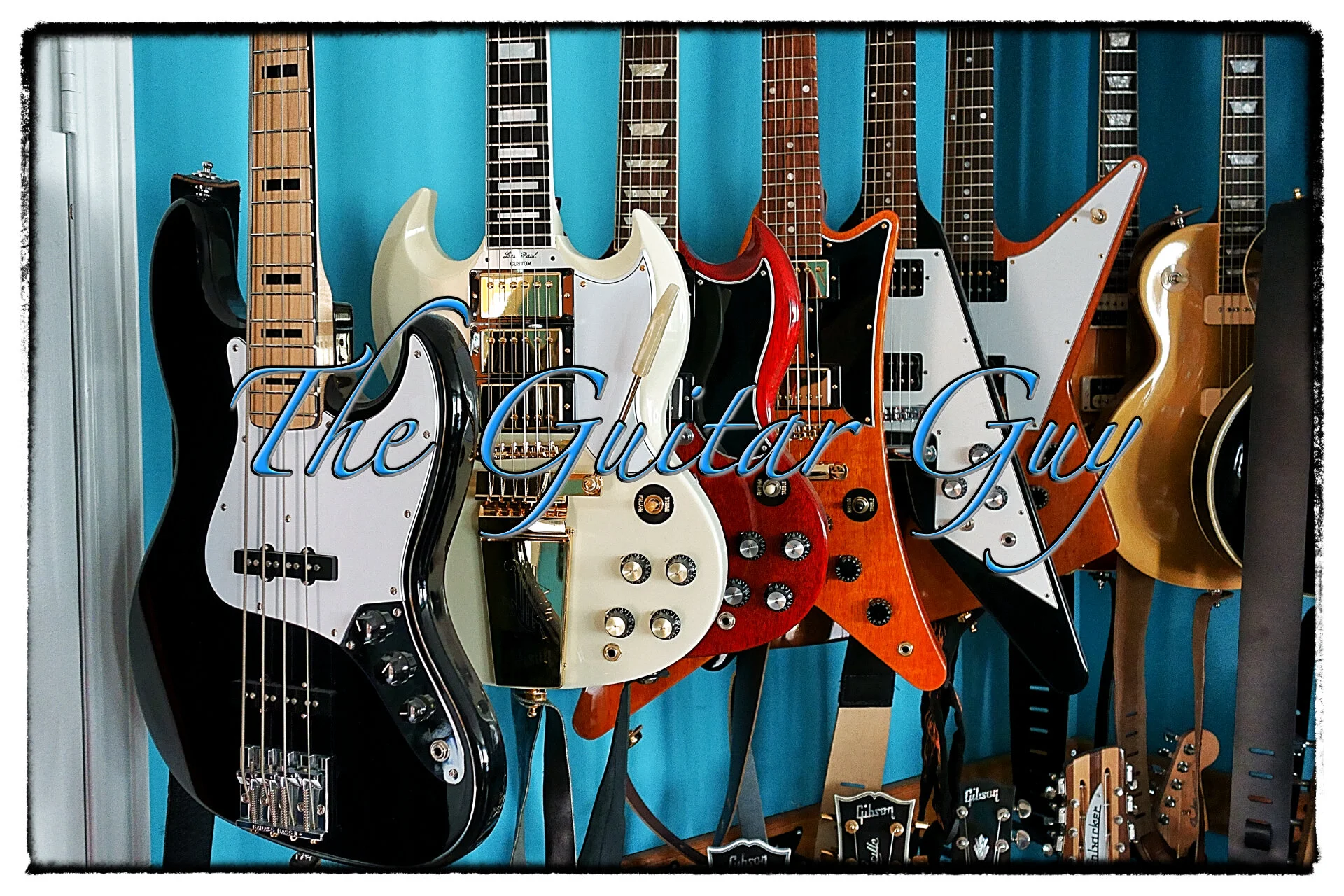
Restringing a Rickenbacker 12 string / How to become an alcoholic
I was at my local guitar store, The Arts Music Store in Newmarket Ontario chatting with my dear friend, store manager, Archy Hachey this past Saturday. We’re of a similar generation and he asked what excitement I had planned for my evening. I told him I was going to be restringing a 12 string because the strings that I had ordered special for it had arrived in the mail. Archy, being the knowledgeable gent that he is noted that doing so is what he calls a four fingers job, making the gesture for four fingers of fine single malt Scotch.
The guitar in question is my Rickenbacker 381/12v69 12 string. Ric 12 strings are strung with the pairs reversed compared to other twelve strings which helps give them their rather distinctive sound. The 381V69 is nominally thicker and heavier than the more widely known 360/12 and has a double bound body and lacks the rounded edges. The maple top and back are highly figured, mine showing a lovely birdseye figure. The necks are a traditional Rickenbacker dual truss rod style and the headstock is the classic Rickenbacker 12 setup with 6 tuners out the sides and 6 tuners out the back. That means six use traditional posts and the other six use the roller type one finds in a slotted headstock. Ric slotted headstocks are only open on the front however, and I will come back to that.
You can see the headstock clearly in this image from the Toronto shop The 12th Fret at www.12fret.com
I’ve owned the guitar for probably twenty years and never played it much. It needs a bright and clear amplifier and the narrow fretboard combined with my sausage fingers never seemed to go anywhere. In fairness, I also didn’t make a big effort at the time because I was in one of collecting binges. So it hung there on the wall. The strings were fresh when I bought it, and were age dead rather than corrosion dead. I decided I was willing to put the time in on it and discovered that Rickenbacker recommended a wound third string instead of plain. A quick perusal of my string inventory as well as some online work and I found that I would need to order some.
I discovered a shop on the net called Pick of the Ricks. They do all things Rickenbacker so I ordered two sets of Rickenbacker branded strings and one set of custom made Curt Mangan strings made for the 12 string electric Rickenbacker. They arrived in a reasonable time and at a fair price. I only later learned that I could get the Rickenbacker branded strings locally in Canada from Long & McQuade Musical Instruments. Such is life. I probably could have saved a couple of bucks, but I now know of a really cool Ric related shop.
Prep
I will start off by telling you that you will need some tools that you would expect and some that you would not. If you don’t know where to go for such tools, your better guitar shop may sell some or you can go online to Stewart-MacDonald, which is what I did a long time ago and all those tools still work today.
Guitar polish
Nut and saddle lube
#0 Phillips screwdriver
3/32 flat blade screwdriver
Fingerboard guards
0000 Steel wool
String Winder
Side Cutters
Electrical contact cleaner
Straight edge or relief gauge
Truss rod wrench
10mm wrench
Super fine flat file
Fine polishing tape
Long nose hemostats
Dental mirror
Gaffer tape
Ok, let’s get started. Unwind the old strings. When they are loose enough, they will be easily dislodged from the R tailpiece. Often they will just fall out. Make note of this, it will bite you later. Use your side cutters to cut the strings near the nut so you don’t take your eye out trying to remove them, especially the ones on the tuners in the headstock slots. Needle nose pliers will be a help, but I strongly recommend a set of long nose locking hemostats for this purpose. You can find such things on Amazon. Orient the holes in the tuners as you normally would for the top facing posts, and follow the guidance in the video linked below for Bill Baker’s Three Finger Method for the tuners in the headstock slots.
Use your Phillips screwdriver to remove the bridge cover and the truss rod cover and don’t lose the screws.
Now’s a good time to clean everything. Use your small flat bladed screwdriver to loosen the grub screws holding the knobs on the pots, remove the knobs and stow them in proper order. I use a small amount of electrical contact cleaner sprayed into each of the pots and into the pickup switch. I then work the pots and the switch a fair bit. It’s pretty amazing how much smoother that they will get. I put some cloths around the pots and the switch to avoid getting the contact cleaner anywhere else.
Next take your relief gauge or straight edge and check the neck. Unlike other guitars you cannot remove the truss rod cover when the strings are on because they ride on it. Even if you could, you wouldn’t get a truss rod wrench onto either of the truss rod nuts with the strings on anyway. Perform your truss rod adjustments as necessary. If this sounds like a black art to you, there are good tutorials over at stewmac.com Seriously, this is a skill all guitarists need to be comfortable with.
Ok. Now screw that truss rod cover back on. Take some guitar polish and spray it on to a clean microfibre cloth. I use Jim Dunlop Formula 65 because I find it cleans up quick, has no abrasion and doesn’t build up. Clean the body and the fretboard. This is a lacquered fretboard so not a place for fretboard oils and such. Just use the polish and scrub that board with that non-abrasive cloth. Now fit your fingerboard guards to isolate each fret and polish them with the 0000 steel wool. If you do not have fingerboard guards, gaffer tape works. You can of course buy fret board polishers and even wheels for your Dremel but if your guitar is in even vaguely good shape, steel wool does a good job. Once all the frets are done, come back with more polish and a clean section of cloth and clean up the detritus. You may be surprised how much there is. At this point, I go a step further every few years. I put a bit of Autosol on a soft felt wheel and with fingerboard guards in place, gently run the wheel in a small Dremel over the frets. This not only polishes them a bit more, but it also works to protect the frets a bit. Be gentle and use the Autosol sparingly. If your top facing tuners have hold down nuts, tighten them up with your wrench. You do not need to tighten them excessively, just so they are not loose. My guitar in this case has no such nuts so I do not have to do this.
Take an old dry toothbrush to the nut and to the bridge. The bridge is not anchored in place so be sure it does not slide all over the guitar top. With a magnifier inspect the nut for excessive wear. If the guitar was playing well already, the cleaning of the slots is all you will likely need to do. My experience is that the saddles on Ric bridges are very rough. I like to take a very fine file and just clean up any burrs or such near the string notches. It’s a small thing but makes a difference.
This is also a good time to take that fine abrasive tape and do a couple of passes on the tuning rods in the slots on the headstock. I have encountered one that had a burr on the edge of the hole that was hard on the string. Takes about 5 seconds per post.
Wipe down everything that you filed. Now prep it for strings by applying a lube of our choice. Whether you use a commercial product such as Nut Sauce or powdered graphite is up to you, but be sure to apply some lube to the now clean nut slots and to the string notches in the bridge.
Reinstall the potentiometer knobs and tighten them so they are sitting a bit proud of the deck so they do not bind. Place your guitar on a stable flat surface with a neck rest. I built my own, but you can also buy commercial ones. I have an old heavy ironing board that I cover with a piece of carpet underlayment for my work surface. It helps prevent the guitar and neck rest from sliding around, and the height of the ironing board means that I am not bent into a position that is going to give me neck or back strain.
And Now Alcoholism
I am convinced that the original engineers were drunk when they designed the stringing method for R tailpiece 12 strings. Or that they had a massive amount of malicious intent. My guitar has the R tailpiece. It looks fab. Architecturally it is an instrument of torture which is why the answer to how to restring an R tailpiece question has the typical answer of replace it with a trapeze model. I want to keep the R. The problem is that the R is only accessible from the bottom and the string slots and ball notches are irregular on their best days. By irregular, I mean that the slots are of varying widths not aligned to string demands and that the ball notches are more like “it might notch, but probably won’t, and the string will fall out at any time until fully tensioned”. I tried following the methods on YouTube videos. Frankly this resulted in profuse sweating, the use of creative metaphors at some volume in a variety of human and Klingon dialects (it’s important to know how to swear in multiple cultures), and a broken high A string after having to redo it several times. So my Ric has a high A from an Elixir 12 string set.
I have come up with a process to restring Ric 12 strings and will now be happy to do it for a fee for any local owners who have decided that heroin abuse is not a path that they wish to take. Here’s the deal. Note that the amount of Writer's Tears Irish Whiskey required to develop this method is not shared.
I presume that you have all the old strings off. If you skipped the section called Prep, go back and read it, because there are tools that you are going to need noted there.
An R tailpiece is actually two pieces. There is the part that is anchored to the guitar and the R itself which comes off when there is no tension on it. Most of us restring one at a time. Doing so is an exercise in frustration with an R tailpiece. Take it off and place it on a stable surface with lots of space upside down. Open each pair of strings, and place them in the proper slot and the ball in the proper notch. Rotate the string so the barrel of the ball end is parallel to the face of the notch. If you do not do this, strings are highly likely to pop out. Put some tension on the string to try to seat the ball in the notch. Do not be surprised when this only works marginally.
Take your time and load all the strings in the tailpiece and let them rest on your work surface. Remember I mentioned that you will need space, because you do not want to bend or kink the strings. Use a magnifier and a light to confirm that all the balls are properly in their notches. Then check twice more, because if the strings pop out when the tailpiece is mounted, you will wish that you had six inch long ⅛ inch wide sticky tipped alien fingers and the ability to rest an eyeball on the top of the guitar so you can see upside down. A dental mirror is a reasonable substitute. If you don’t have a mirror, you probably did not read the prep section. Avoid having to use this by employing the musician and photographer’s best friend, a roll of gaffer tape. Gaffer tape is NOT duct tape. Buy some from your music or camera store or get it on Amazon. Gaffer tape sticks well but also comes off well and leaves no residue behind.
Once your strings are in the tailpiece, take a piece of gaffer tape and wrap it starting on the bottom around the back of the R opening and then across the top of the R in a U shape to hold the strings in the slots and the balls in the notches. Take the time to ensure that it holds things in place, or trust me, you will regret not doing so later.
Now flip the tailpiece over and mount it on the guitar. It will not lock in place until there is string tension, so use some more gaffer tape to hold it to the mount.
Now step away and take a short break.
Come back and check twice to ensure that the right strings are in the right slots and that everything looks right. Remember that Ric 12s have the pairs oriented in reverse to all other 12 strings. Now head over to Bill Baker’s video on his three finger method for handling the strings that go on the tuners inside the slots. I found this too late and it will make your life easier and avoid the strings going slack when you are winding them on and thus reduce the likelihood of a string break.
My method involves winding on all the strings that go into the slotted headstock tuners first. I found that doing them in order was a pain. Bill also recommends working from the outside in and I support this method, so go E A D, then E B G. Wind them on so they are snug, but not up to tune. Then go on to the strings that wind onto the upward facing posts. Give yourself enough slack on these guys to get at least three winds on the post. I tend to put an L in the string about 1.25” past the post and use that as a guide. Bill likes to lock his strings, I don’t do this, you should do whatever you are comfortable with but be sure to get those three winds on the post or you may not like the sound.
Once you are assured that the strings are sitting in the proper saddle position in the bridge and are tense enough not to move, replace the bridge cover.
Now tune up, and you will probably find it easiest to alternate sides, doing the low Es first then the high Es, then the As etc. Now go through whatever your normal stretching interval is and retune. Play fairly aggressively and retune. I found that with the Rickenbacker branded strings, my normal stretching method required four retunes before the strings held. This is more than I am used to but again, not a big deal.
You are now ready to play. Find some Byrds or Tom Petty or whatever and have at it. Don’t forget that bright clean channel and buckets of reverb!